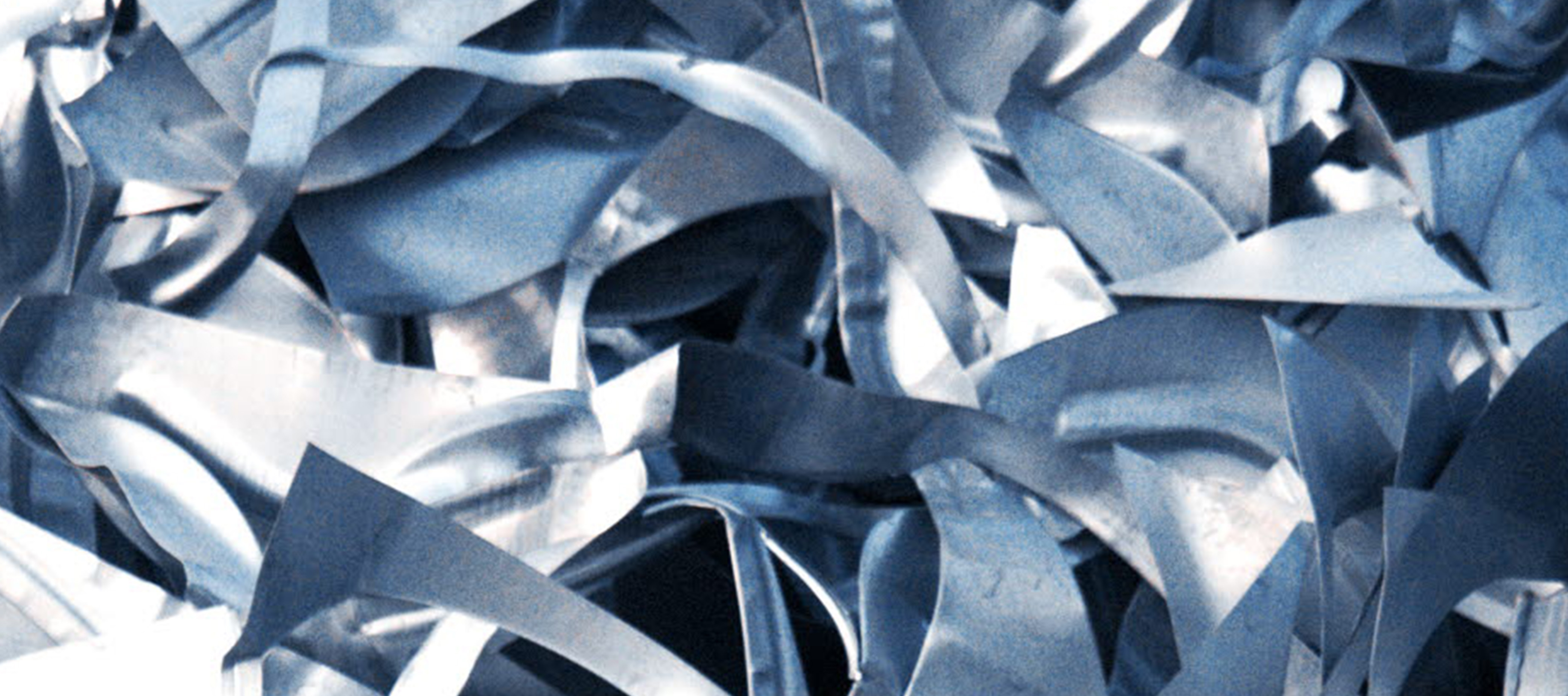
Lindéngruppen company, Höganäs, is switching to secondary raw materials in metal powder production to reduce both costs and carbon emissions.
The Höganäs atomising plant in Halmstad, Sweden, works to incorporate increasing amounts of secondary raw material in its metal powder production process. It involves incorporating secondary raw materials in a cost-effective way and overcoming challenges to ensure quality of materials.
At the plant in Halmstad, Höganäs are working to entirely replace virgin materials with steel scrap. The team now uses 99 per cent secondary material to produce steel powder in their Electric Arc Furnace and continue their work to replace the remaining virgin alloying materials with scrap. This strengthens Höganäs’ market position by reducing its indirect carbon dioxide emissions, production costs and energy consumption.
“The scrap blend is converted into liquid steel and then dispersed into small particles with the help of high-pressure water, instead of being continuously casted into billets/slabs as on conventional steel plants,” explains Mikhail Lukin, Smelting Manager at the Atomising Plant in Halmstad.
To incorporate more secondary materials in the process, Höganäs has altered their refining processes to overcome challenges related to removing impurities. They have also placed stricter demands on their scrap supply chain for both existing and new suppliers.
“We were forced to learn new ways of working with steel refining, completely changing old views and habits,” says Charlie Wedell, Site Manager at Halmstad.
“We have learned a lot from transitioning to a fully scrap-based production. We used to think it was impossible to blend-in lower quality scrap without sacrificing the quality of the product. But it was easier than expected,” says both Mikhail Lukin and Charlie Wedell.
The plant in Halmstad annually produces up to 220,000 tonnes of iron powder, which is mostly used by the automotive industry. The scrap used in Höganäs’ process is sourced from the automotive industry as well as from structural steel and consumer goods recycling.